排污泵,这一污水处理与排放的核心设备,在现代工业与城市建设中占据着举足轻重的地位。面对市场上琳琅满目的排污泵品牌与型号,如何挑选一款既符合实际需求又性能稳定的排污泵,成为了众多用户关注的焦点。中成泵业,作为业内知名的泵类设备供应商,其排污泵产品在市场上广受好评。
在选型过程中,我们首先要关注的是污水流量与排放高度。不同的应用场景对排污泵的流量和扬程要求各不相同。因此,在选型时,我们必须准确掌握现场数据,确保所选排污泵的规格与实际应用相匹配。过大或过小的泵都可能导致运行不稳定或能源浪费。其次,我们要考虑污水中的介质特性。污水中的杂质、颗粒大小、腐蚀性等因素都会对泵的性能产生影响。因此,在选择排污泵时,必须充分了解介质的性质,选择具有耐磨、耐腐蚀特性的泵体材料和密封方式,以确保泵的长期稳定运行。此外,安装环境也是选型过程中不可忽视的因素。不同的安装位置、空间大小以及电源供应条件,都会对排污泵的选择产生影响。例如,在空间有限的场所,我们可以选择立式排污泵,以节省空间;而在需要频繁移动的场景中,便携式排污泵则更为合适。
在应用领域方面,排污泵广泛应用于城市排水系统、污水处理厂以及工业废水处理等领域。无论是城市雨水的排放,还是工业废水的处理,排污泵都发挥着至关重要的作用。它不仅能够高效地将污水输送到指定地点,还能确保污水处理过程的顺利进行,为环境保护和工业生产提供了有力保障。在使用排污泵时,我们也需要注意一些事项。定期对排污泵进行检查和维护是必不可少的。这不仅可以确保泵的正常运行,还能及时发现并解决潜在问题,延长泵的使用寿命。在运行过程中,我们要确保泵内有足够的介质,避免干转导致泵体损坏。同时,合理控制运行负荷,避免过载运行对泵造成过大的负荷。
选择合适的排污泵对于污水处理与排放至关重要。通过深入了解排污泵的选型原则、应用领域以及使用注意事项,我们能够更好地掌握这一设备的应用技巧,为环保事业和工业生产贡献自己的力量。而中成泵业作为行业内的知名品牌,其产品在性能与品质上均有着不俗的表现,值得我们信赖与选择。
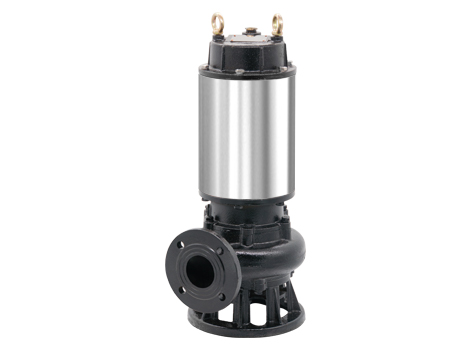